Biomass Fired Boilers
Biomass Fired Boilers designed to meet the growing demand for sustainable and cost-effective energy (Steam & Power) solutions. These boilers utilize renewable organic materials (biomass fuel) such as rice husk, cashew shall, ground nut shell, mustard husk, bagasse, wood chips, cotton stalks, and other agro-waste to generate low/high-pressure steam for industrial processes and power generation — while significantly reducing carbon emissions.
Our boilers are equipped with advanced combustion systems, air-fuel control, and ash handling mechanisms to deliver consistent performance with minimal manual intervention, making them ideal for industries aiming to switch to renewable fuel sources without compromising on reliability or efficiency.
Capacity
2 TPH to 200 TPH
Work Pressure
Up to 110 kg/cm²
Temperature
Up to 515°C (Superheated Steam)
Fuel Options
Wood chips, Rice husk, Rice straw/Cane trash (Chipped/Bales), Sawdust, Bagasse, Groundnut shell, Cotton stalk, Palm kernel shell, Mustard husk, and other biomass-based fuels (briquettes/pellets) etc.
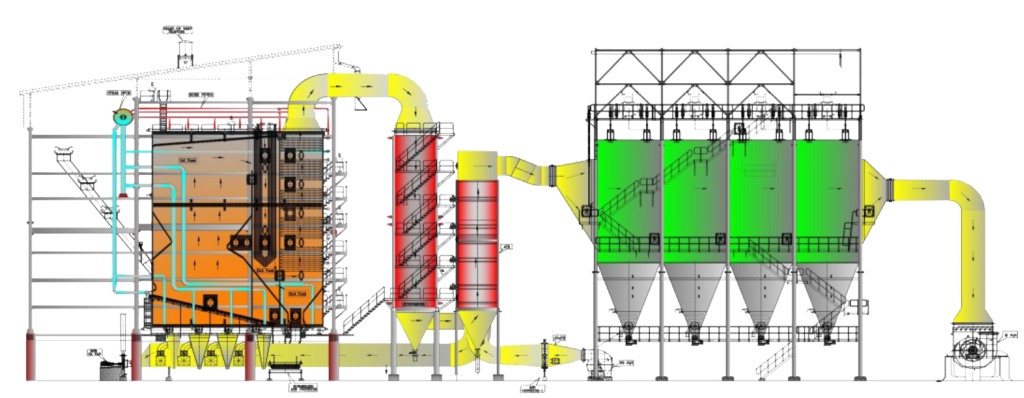
Biomass combustion is carried out in specially designed furnaces that ensure efficient burning, high heat transfer, and low emissions.
Biomass Boilers can be distinguished or featured by Firing Options:
- Pin Hole Grate
- Vibrating grate
- Travelling Grate
- Dumping Grate
- Pulsating/Reciprocating Grate
- Atmospheric Fluidized Bed Combustion (AFBC)
With Smoke Cum Watertube or Watertube Single/Bi-Drum configurations. Handles 100% biomass fuels in bale, briquette, or loose form.
Design & Operation:
Water-tube or fire-tube configurations with reciprocating/vibrating grate technology for efficient combustion.
Handles 100% biomass fuels in bale, briquette, or loose form (e.g., rice husk, cane trash, cotton stalk).
Multi-pass flue gas flow to maximize heat recovery and minimize choking.
Compliance: IBR-certified, integrates with ESPs, cyclones, or scrubbers to meet CPCB emission norms.
Biomass combustion is carried out in specially designed furnaces that ensure efficient burning, high heat transfer, and low emissions.
Biomass Boilers can be distinguished or featured by Firing Options
- Pin Hole Grate
- Vibrating grate
- Travelling Grate
- Dumping Grate
- Pulsating/Reciprocating Grate
- Atmospheric Fluidized Bed Combustion (AFBC)
Pressure & Process Boilers introduce Rice Straw Bale Fired water tube Boiler to Generate the steam for Process and Power generation at minimum Running Cost The proposed boiler is a Single-Drum Water Tube Boiler with multi-pass furnace design with Internal Super heater.
The boiler is design to burn 100% Rice straw in Bale shape or any Biomass. The Rice straw contains Silica, K 2 O and oxides of Sodium and magnesium which are harmful for life of Boiler too. Keeping in view the impurities and high alkali contain in fuel, the boiler is specially designed to avoid Fouling/Slogging problems.
Technology: The Boiler equipped with Reciprocating Grate / Vibrating Grate Technology to Brun the 100% Rice Straw with maximum Free Board Area and multi pass Design to avoid the Choking of Boiler. The flue gases then pass-through multi-furnace zone and major ash particles are separated at grate outlet. The flue gases then pass through Super heater evaporator section after that Economizer, Air Pre Heater, and Cyclone Bag House/ESP. The system is equipped with number of customized soot blowers for on-line cleaning.
Key Points
- Fuel Flexibility & Versatility: Burns diverse biomass fuels, including dry and moist agro-waste, wood-based fuels and other industrial residues.
- Clean Energy Solution: Biomass is carbon-neutral and helps reduce reliance on fossil fuels while complying with environmental norms.
- High Thermal Efficiency: Advanced combustion design (Reciprocating/vibrating grates) and heat recovery systems ensure optimum fuel utilization and lower operating costs.
- Rugged Construction: Manufactured using high-quality (grade) materials to ensure long service life, durability, and low maintenance needs.
- Low Maintenance & Easy Operation: User-friendly design with accessible components, modern controls, and minimal downtime.
- Custom Engineered Designs: Tailored boiler systems to suit your specific fuel availability, load requirements, and space constraints.
- Efficient Ash Handling: Integrated systems for smooth removal and management of ash and unburned residues.
- Cost Effective: Reduces fuel costs by using low-cost agro-waste
- Fuel Flexibility: Burns diverse biomass fuels, including agro-waste and industrial residues.
- Advanced Grate Systems: Reciprocating/vibrating grates ensure complete combustion.
- High-Pressure Steam: Supports power generation and heavy industrial processes.
- Emission Control: Compatible with ESPs, mechanical dust collectors, and wet scrubbers.
- Multi-Pass Design: Prevents boiler choking and enhances heat transfer.
- IBR Certification: Complies with Indian Boiler Regulations for safety and reliability.
- Automated Feeding: Continuous fuel feeding systems for uninterrupted operation.
- Low Maintenance: Robust construction with studded in-bed coils for durability.
- Retrofitting: Upgrades for existing boilers to improve efficiency or switch fuels.
- Global Installations: 130+ boilers installed across India, Pakistan, and Canada.
Applications
- Sugar Plants: Bagasse-fired steam for milling and power generation.
Distilleries: Spent wash/vinasse combustion for process heat.
Paper Mills: Biomass steam for pulping and drying.
Plywood Industry: Hot pressing and glue curing.
Textiles: Dyeing, drying, and steam conditioning.
Chemicals: Reactor heating and solvent recovery.
Rice Mills: Husk-fired steam for parboiling.
Food Processing: Sterilization and packaging.
Cement Plants: Waste heat recovery and auxiliary power.
Solvent Extraction: Steam for oilseed processing.
Salient Features
- Furnace Design: Different furnace designs for different fuels.
- Multi-Pass Flue Gas Flow: Enhances heat recovery, reduces choking, and increases efficiency
- High-Pressure Steam: Supports power generation and heavy industrial processes.
- Carbon Neutral: Sustainable alternative to fossil fuels, lowering carbon footprint.
- High Efficiency: Multi-pass flue gas flow and heat recovery systems maximize output.
- Versatility: Suitable for captive power plants, co-gen, and process steam.
- 24/7 Operation: Automated controls ensure reliable performance.
- Durable Construction: Stainless steel superheaters for fouling fuel.
- Retrofitting: Upgrades for existing boilers to improve efficiency or switch fuels.
- IBR Certification/Compliance: Built in compliance with Indian Boiler Regulations, ensuring safety and operational reliability. Meets IBR, ISO, and CPCB standards.
- Emission Control Systems: Integrated with ESPs, cyclones, bag filters, or scrubbers to meet CPCB norms for SOx, NOx, and particulate matter.
- Automated Operation: PLC-based control systems with real-time monitoring and continuous fuel feeding for uninterrupted performance
PPB’s boiler is design to burn 100% Straw in Bale form or any Biomass. The Rice straw contains Silica, K₂O and oxides of Sodium and magnesium which are harmful for life of Boiler too. Keeping in view the impurities and high alkali contain in fuel, the boiler is specially designed to avoid Fouling/Slogging problems.
With our expertise in thermal engineering and process integration, Pressure & Process Boilers Pvt. Ltd. offers Biomass Fired Boilers that are economical, environmentally responsible, and designed for long-term performance. Whether you’re looking to utilize agro-waste or industrial by-products as fuel, we provide reliable and customized solutions that help industries move toward greener energy goals.
- Cost-Effective: Uses low-cost agro-waste, reducing fuel expenses.
- Carbon Neutral: Sustainable alternative to fossil fuels, lowering carbon footprint.
- High Efficiency: Multi-pass flue gas flow and heat recovery systems maximize output.
- Scalability: Modular designs for easy capacity expansion.
- Compliance: Meets IBR, ISO, and CPCB standards.
- Versatility: Suitable for captive power plants, co-gen, and process steam.
- Reduced Ash Handling: Advanced grate systems minimize unburnt residue.
- 24/7 Operation: Automated controls ensure reliable performance.
- Durable Construction: Stainless steel superheaters and corrosion-resistant materials.
- After-Sale Support: PP Boilers provides audits, training, and maintenance.