SPARES
Compliance
IBR-certified and ISO 9001:2015 compliant
Pressure Parts
Operating pressure up to 120 kg/cm²
Fans (FD, ID, PA)
Flow rates up to 500,000 m³/hr
Temperature
Up to 540°C (for superheater coils)
Details
PP Boilers provides a comprehensive range of spares tailored to support boiler operations and minimize downtime. These components are integral to maintaining efficiency, safety, and compliance in industrial processes. Key categories include:
- Fans: Forced Draft (FD), Induced Draft (ID), and Primary Air (PA) fans for optimal airflow and combustion.
- Pressure Parts: Studded in-bed coils, superheater coils, and economizer coils for efficient heat transfer.
- Pollution Control Equipment: ESP components, scrubber parts, and dust collector elements.
- Structural Components: Expansion bellows, air pre-heaters, silencers, and support structures.
Key Points
- Essential for enhancing productivity and efficiency in various industries.
- Available in a wide range of types and specifications to meet diverse needs.
- Regular maintenance is crucial for optimal performance and longevity.
- Can be integrated with other systems for improved functionality.
- Safety features are often included to protect operators and workers.
- Equipment can be customized based on specific operational requirements.
- Advances in technology have led to more energy-efficient and automated options.
- Training is often required for proper operation and safety compliance.
- Equipment can significantly reduce manual labor and associated risks.
- Supports compliance with industry standards and regulations.
Features
- Reliability: Ensures continuous boiler operation with minimal downtime.
- Cost-Effectiveness: Reduces long-term maintenance and replacement costs.
- Enhanced Efficiency: Optimizes combustion and heat transfer processes.
- Emission Compliance: Supports adherence to environmental regulations.
- Durability: Long service life due to robust construction and premium materials.
Applications
- Power Generation: Replacement fans and coils for steam boilers.
- Cement Plants: Dust collector components for emission control.
- Steel Mills: Structural spares for high-temperature processes.
- Chemicals: Heat exchanger coils and expansion joints.
- Textiles: Silencers and air pre-heaters for drying systems.
SPARES
NON-PRESSURE PART
Accordion content goes here!
PRESSURE PARTS
TUBE/PIPE
– Water walls / Furnace Tubes: SA 210 Gr A1/Gr C, SA 192, SA 106 Gr B, SA 213 T11/T22, SS 304/316
– Superheater / Reheater: SA 213 T11/T22/T91, SS 304H, SS 321, SS 347H
– Economizers: SA 210 Gr A1/Gr C, SA 106 Gr B, ASTM A179, ASTM ERW A53 Gr B, SA 213 T11/T22, SS 304/316/321
– Steam Headers: SA 106 Gr B/Gr C, SA 335 P11/P22/P91, SS 304H, SS 321, SS 347H
– Feedwater Piping: SS 304 / 316, A106/SA106 Gr B/C, SA 210 Gr C, ASTM A53 Gr B ERW, SA 335 P11/P22/P91, SS 304/316/321, SS 347H
– Steamline: SA 106 Gr B/Gr C, SA 335 P11/P22/P91, SS 304H/321/347H
All boiler tubes and pipes supplied by PP Boilers conform to stringent international and national codes, including:
ASME Section I & VIII
ASTM A213, A335, A106
DIN EN10216/10217
IBR (Indian Boiler Regulations) – with third-party inspection and stamping where applicable
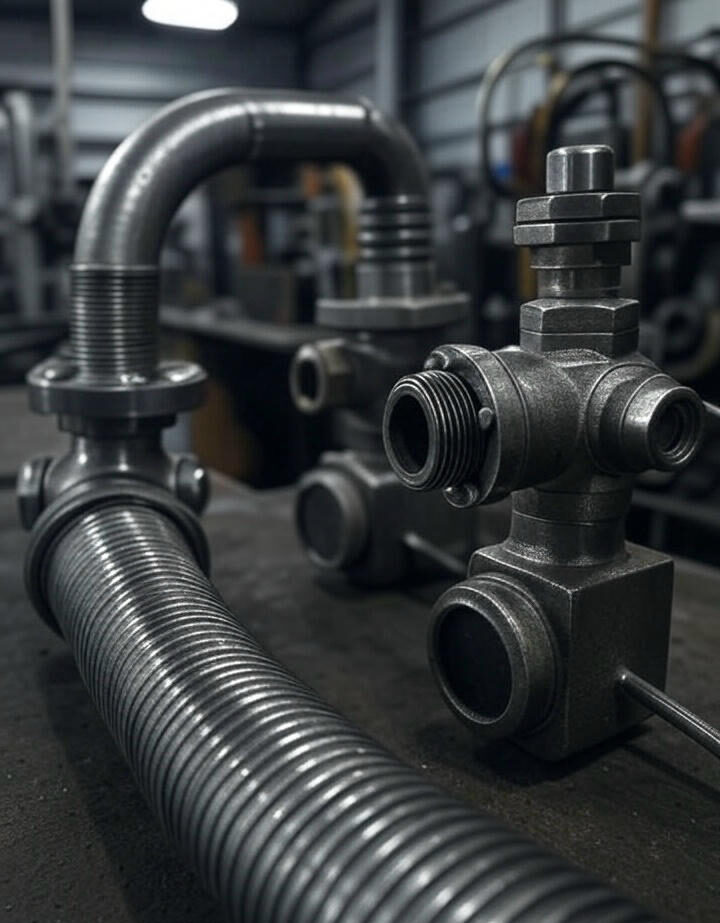
TUBE/PIPE
– Water walls / Furnace Tubes: SA 210 Gr A1/Gr C, SA 192, SA 106 Gr B, SA 213 T11/T22, SS 304/316
– Superheater / Reheater: SA 213 T11/T22/T91, SS 304H, SS 321, SS 347H
– Economizers: SA 210 Gr A1/Gr C, SA 106 Gr B, ASTM A179, ASTM ERW A53 Gr B, SA 213 T11/T22, SS 304/316/321
– Steam Headers: SA 106 Gr B/Gr C, SA 335 P11/P22/P91, SS 304H, SS 321, SS 347H
– Feedwater Piping: SS 304 / 316, A106/SA106 Gr B/C, SA 210 Gr C, ASTM A53 Gr B ERW, SA 335 P11/P22/P91, SS 304/316/321, SS 347H
– Steamline: SA 106 Gr B/Gr C, SA 335 P11/P22/P91, SS 304H/321/347H
All boiler tubes and pipes supplied by PP Boilers conform to stringent international and national codes, including:
ASME Section I & VIII
ASTM A213, A335, A106
DIN EN10216/10217
IBR (Indian Boiler Regulations) – with third-party inspection and stamping where applicable
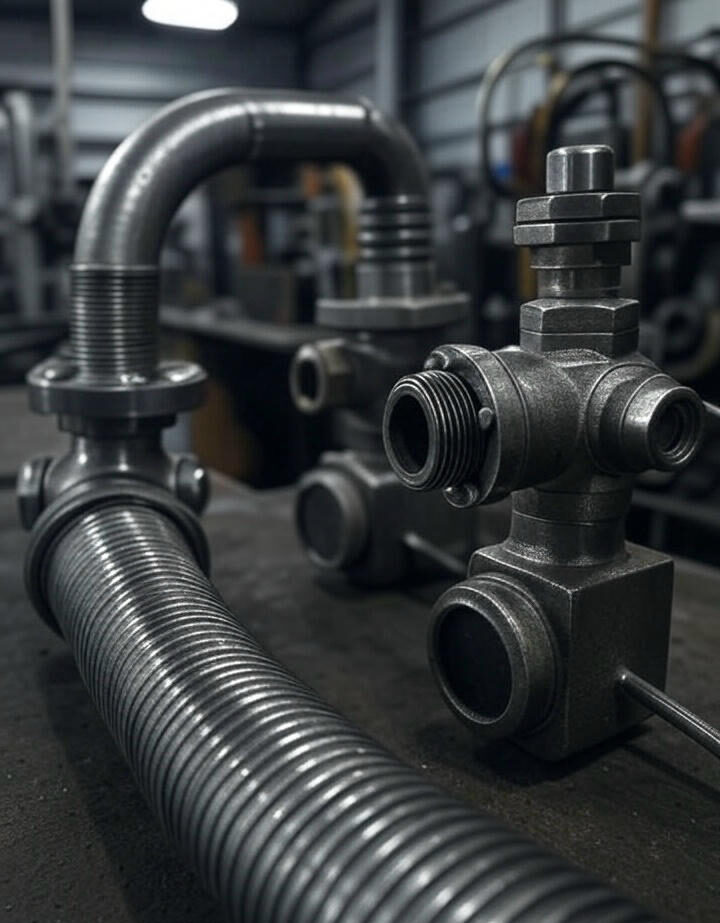
VALVES
Categories & Specifications:
- Gate Valve
- Globe Valve
- Ball Valve
- Butterfly Valve
- Plug Valve
- Pneumatic Globe Control Valve
- Pneumatic Ball Valve
- Pneumatic Butterfly Valve
- Motorized Gate and Globe Valve
- Motorized Ball Valve
3. Motorized (Electric) Valves:
- Motorized Gate and Globe Valves
- Motorized Ball Valves
4. Safety & Relief Valves:
- Spring-Loaded Safety Valves
- Pilot-Operated Valves
- Thermal Relief Valves
- Spring-Loaded Safety Valve
- Pilot-Operated Valve
- Thermal Relief Valve
- Lift Check & Swing Check Valve
- Non-Return Valve
6. Blowdown Valves:
- Quick-Opening Blowdown Valve
- Continuous Blowdown Control Valve
- Pressure Classes: ANSI 125#, 150#, 300#, 600#, 900#, 1500#, 2500# (selection based on operating conditions).
- End Connections: Flanged (RF, RTJ), Butt Weld, Socket Weld.
- Design Standards: ASME B16.34, API 600, API 602, API 603, BS 1873, IBR compliance.
- Materials: WCB, WC6, WC9, C5, C12A, SS 304/316/321/347, P11, P22, high-temp alloys.
- Trim & Seat Materials: Stainless steel, Stellite-faced, and PTFE options for erosion and temperature resistance.
- Leakage Classes: API Class IV, V, VI, with control valves rated as Class V+ for precise flow control.
- Actuations: Manual, pneumatic, electric motorized, optional hydraulic.
- Fire Safe Design: Conforms with API 607 for fuel/gas services.
All valves are rigorously tested per API 598 standards, ensuring performance, safety, and long service life across diverse boiler applications. Customization in sizes, end connections, and actuation options is available to meet specific project requirements.
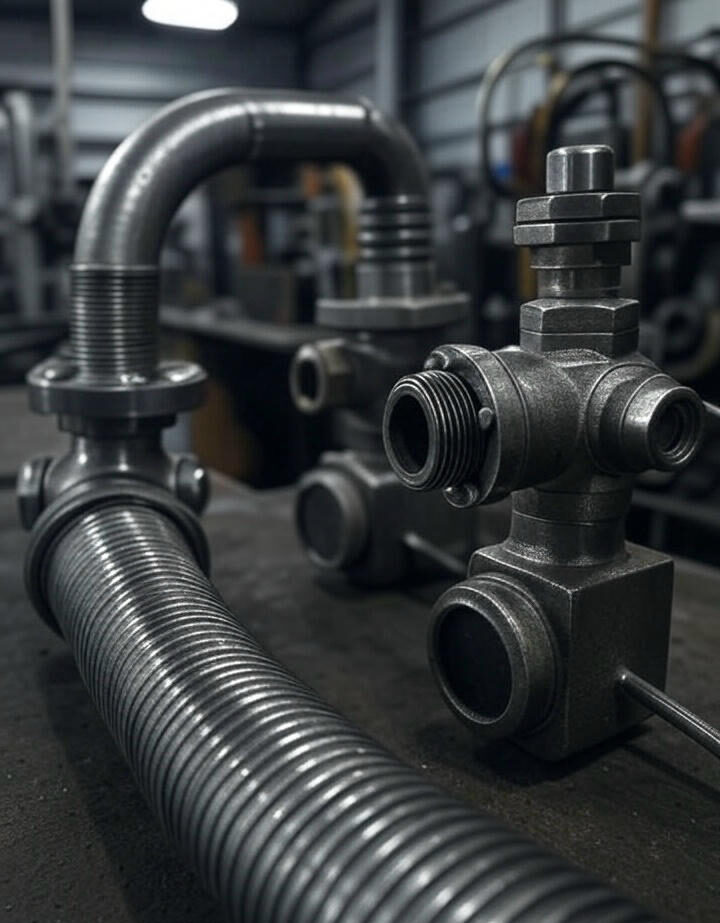
COILS
PP Boilers specializes in the design, fabrication, and supply of high-performance boiler coils engineered to meet the demanding thermal and mechanical requirements of modern industrial boilers. Our range includes Studded In-Bed Coils, Economizer Coils, and Superheater Coils, each tailored for specific zones within the boiler system to maximize heat transfer, reliability, and efficiency.
Boiler Bed Coils (Fluidized Bed Coils / Bed Evaporators)
Studded In-Bed Coils are critical heat transfer elements embedded within the fluidized bed of AFBC boilers. Designed to operate under high-temperature, high-erosion environments, these coils efficiently extract heat from combusting bed material and transfer it to the working fluid (water/steam). Their studded surface significantly increases the effective heat transfer area and sustains fluidization within the bed.
Design & Construction:
- Constructed from high-grade materials including ASTM A106 Gr. B, A192, SA 210 Gr. C, and stainless steels like SS 304/316
- Tube OD: 25 to 63.5 mm, with wall thicknesses optimized for high-pressure service
- Studs/Fins: Welded MS or SS304 studs to improve heat transfer and protect against erosion
- Surface-treated for resistance to corrosion, erosion, and scaling
- Absorbs direct heat from hot bed material to produce saturated steam
- Promotes stable fluidization essential for efficient combustion
- Helps maintain uniform bed temperature, improving thermal efficiency and combustion control
- Enhances boiler responsiveness during fluctuating load conditions
Performance & Advantages:
- Engineered for long service life under abrasive and cyclic thermal loads
- High thermal conductivity and mechanical strength ensure reliable operation
- Custom-designed for specific boiler capacities and fuel types
- Supports rapid steam generation and efficient load response
- Compliant with ASME Section I, IBR, and client-specific requirements
Economizer coils are integral heat recovery components located in the flue gas path of a boiler. Their primary function is to preheat feedwater before it enters the boiler drum, utilizing residual heat from exhaust gases. This process significantly improves boiler thermal efficiency, reduces fuel consumption, and lowers operational costs. PP Boilers offers custom-engineered economizer coils designed for long-term performance in high-temperature, corrosive environments.
Design & Construction:
- Manufactured using carbon steels like ASTM A106 Gr. B, A179, or A210, and available in low-alloy grades for higher temperature applications
- Tubes configured in bare or finned arrangements to maximize surface area and heat exchange efficiency
- Available in horizontal or vertical coil banks based on space and gas flow direction
- Coil sizes and arrangements are optimized for flue gas temperature, feedwater flow, and pressure drop limitations
- Fabricated as seamless or welded tube assemblies in compliance with ASME and IBR standards
Functions:
- Recovers waste heat from flue gases to raise feedwater temperature
- Reduces the energy required for steam generation by decreasing the enthalpy gap
- Lowers exit flue gas temperature, reducing heat loss through the stack
- Contributes to lower fuel usage and enhanced boiler efficiency (typically by 3–7%)
- Designed for corrosive and high-temperature flue gas environments
- Enhances thermal efficiency and reduces fuel costs
- Prolongs boiler life by minimizing thermal shock and condensation in the economizer zone
- Available with soot blowers or access ports for ease of cleaning and maintenance
- Fully compliant with IBR, ASME Section I, and customer-specific engineering standards
Superheater Coils are critical heat transfer components installed in the convective or radiant zones of a boiler to convert saturated steam into superheated steam. This process increases the thermal energy of the steam, enhancing overall plant efficiency, especially in power generation and high-temperature process applications. PP Boilers manufactures robust, high-performance superheater coils tailored to withstand extreme temperatures, high pressures, and cyclic thermal loads.
- Fabricated from high-temperature alloy steels such as SA213 T11, T22, T91, TP304, TP347H, or stainless steels like SS 304/316, based on operating pressure and temperature
- Available in U-bend, serpentine, and pendant-type coil configurations to suit radiant or convective placement
- Designed for steam temperatures up to 540°C or higher, with pressure ratings exceeding 100 kg/cm²
- Seamless or welded tube construction per ASME Section I, IBR, and customer-specific design codes
- Provision for expansion loops and flexible coil supports to absorb thermal expansion
- Increases the temperature of saturated steam without increasing pressure
- Supplies superheated steam to turbines or process units for improved energy efficiency
- Prevents steam condensation during transport and expansion in turbines
- Enhances heat recovery and thermal performance in power boilers and industrial steam systems
- High thermal conductivity and corrosion resistance for extended operating life
- Optimized coil geometry for uniform heat absorption and reduced metal temperature stresses
- Compatible with fluidized bed, travelling grate, and oil/gas-fired boilers
- Integrated with temperature control systems for precise outlet steam temperature
- Offered with soot blower provisions to maintain clean heat transfer surfaces
- Compliant with ASME, IBR, and ISO standards, ensuring safety and reliability
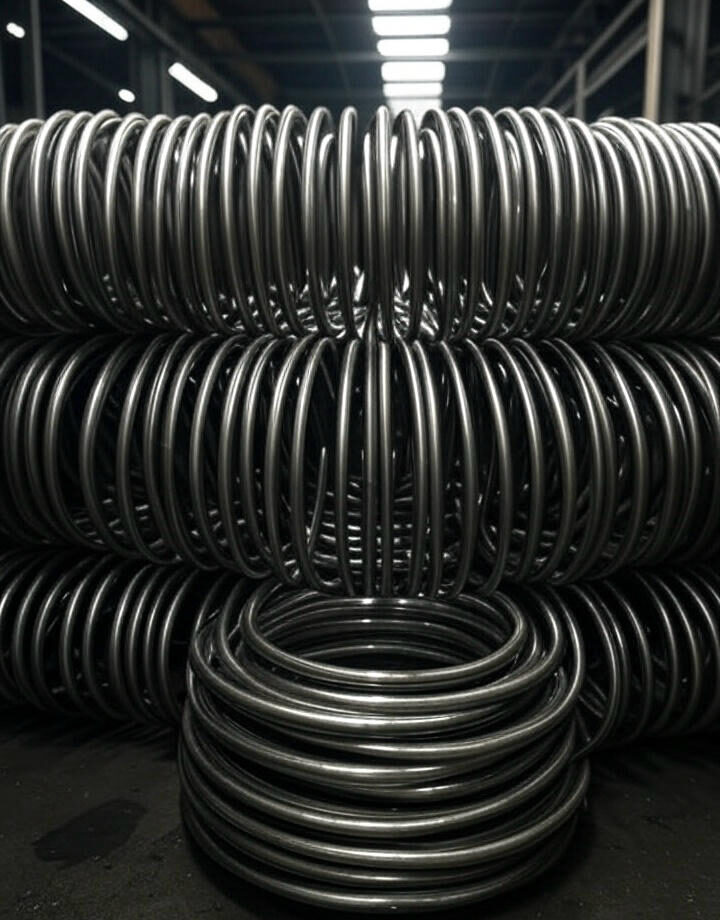
VESSEL
PP Boilers designs and fabricates a complete range of custom-engineered pressure vessels for high-pressure and high-temperature boiler applications. Built to comply with global codes and optimized for reliability and safety, our pressure vessels are integral to the performance of AFBC, CFBC, WHRB and other high-capacity and process boilers.
We offer fully fabricated and IBR-stamped pressure vessels for:
Steam Drum:
Mud Drum:
- Positioned at the bottom to collect sludge and heavy impuritie
- MOC: SA 516 Gr.70, IS 2002, SA 105 flange
- Serve as steam and water manifolds for coil circuits
- MOC: SA 106 Gr. B/C, SA 335 P11/P22/P91, SS 304H/321/347H
- Used to remove dissolved gases from feedwater
- Spray & tray-type available
- MOC: SA 516 Gr.70, SS 304/316 for wetted parts
- Designed to safely discharge boiler blowdown under pressure
- MOC: SA 516 Gr.60/70, with optional refractory lining
- For storing and releasing saturated steam during fluctuating loads
- MOC: SA 516 Gr.70, with suitable insulation and accessories
Design & Code Compliance:
All pressure vessels by PP Boilers are designed as per:
- ASME Section I / Section VIII Div.1
- IBR – Indian Boiler Regulations
- ISO 9001:2015 Quality System
Vessels are supplied with:
- Full NDT testing: Radiography, Hydrotest, UT, MPT
- IBR certification with stamping and form I
- TPI approval from Lloyd’s, TUV, SGS, or as per client requirement
- Diameter Range: 300 mm to 3500 mm
- Design Pressure: Up to 100 kg/cm²
- Design Temperature: Up to 550°C
- Shell Thickness: 10 mm to 80 mm
- Material Options: Carbon Steel, Alloy Steel, Stainless Steel (304, 316, 321, 347H), P11, P22, P91 etc.
Salient Features of Our Pressure Vessels:
- Heavy-duty construction for long life under cyclic and steady-state loads
- High-precision machining of nozzle connections and welding bevels
- Corrosion-resistant internal finishes or claddings available on request
- Fully customizable for layout, nozzle orientation, saddle/base support
- Pre-insulated and cladded supply available for field-ready installation
- Sourced only from Boiler Quality Plates (BQP) with test certificates
- Designed for low maintenance, maximum safety, and thermal efficiency
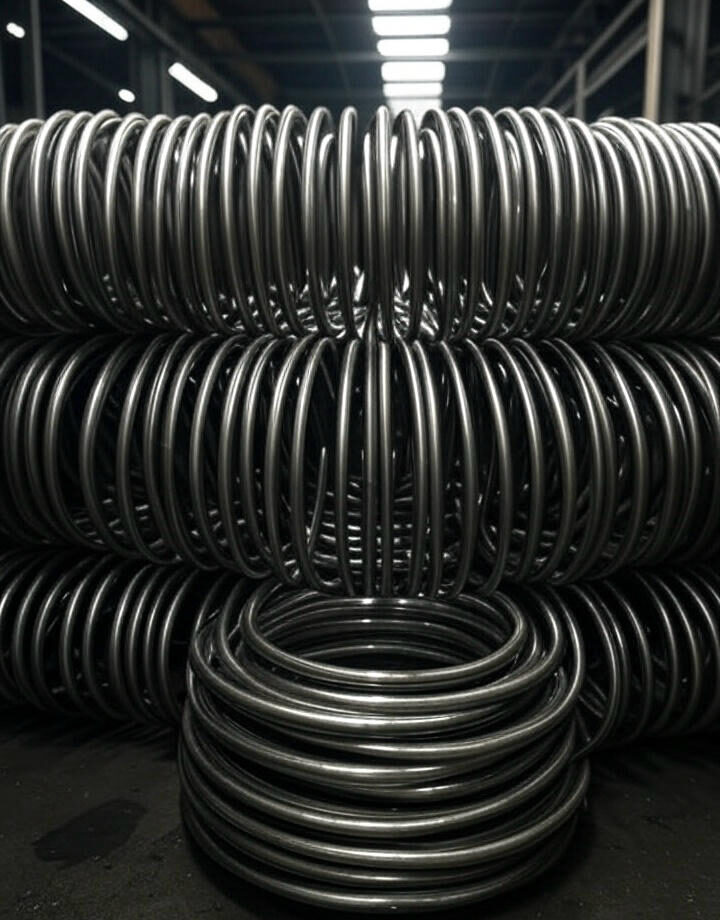
NON-PRESSURE PARTS
TUBE/PIPE (Non-IBR)
We supply high-quality tubes and pipes for non-pressure applications such as ducting, sootblower lances, drain piping, insulation support, and non-process utilities.
- Material Grades: MS, IS 1239, ASTM A106, ERW IS 3589, SS 304/316
- Sizes: ½” to 20″ NB; schedule 10 to 80
- Types: Seamless, ERW, galvanized, or pickled
- Applications: Non-IBR piping, ductwork, expansion loops, instrumentation air lines
Key Features:
- Accurate tolerances and smooth internal finish
- Available with plain, threaded, flanged, or beveled ends
- Surface coating options: painted, epoxy, or zinc
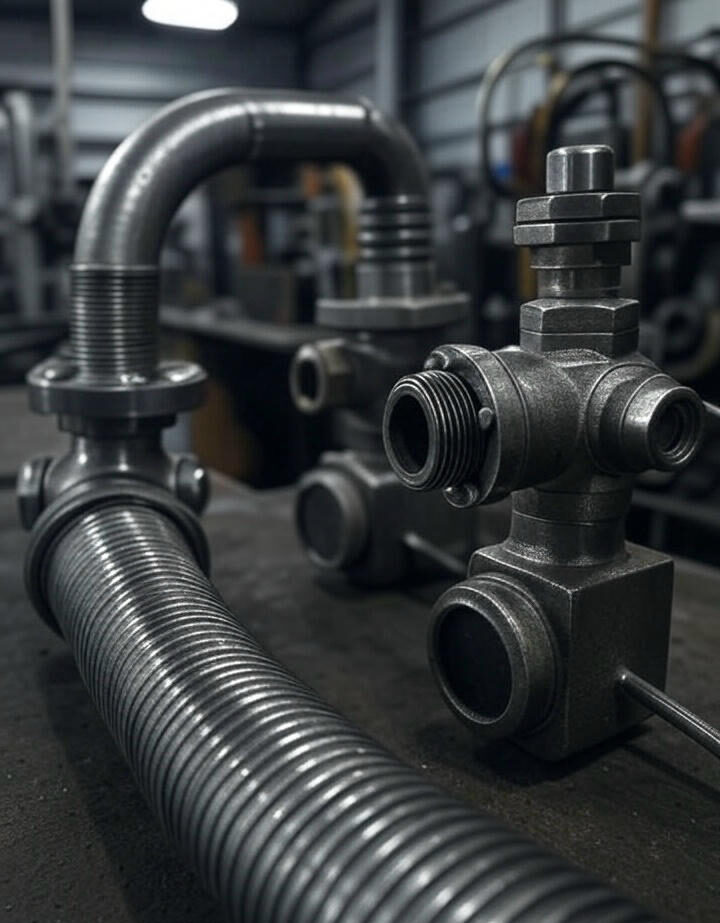
SILENCER
- Types: Vent Silencer, Blow-off Silencer, Safety Valve Silencer
- Material: Carbon steel or stainless steel (internals), MS outer casing
- Design Pressure: Atmospheric to 150 kg/cm²
- Noise Reduction: Up to 40–50 dB(A) depending on application
Key Features:
- Multi-stage acoustic diffusers with absorbent lining
- Designed for zero backpressure and high-velocity exhaust
- Flanged or welded end connections
- Supplied with lifting lugs, weather hoods, and drain traps
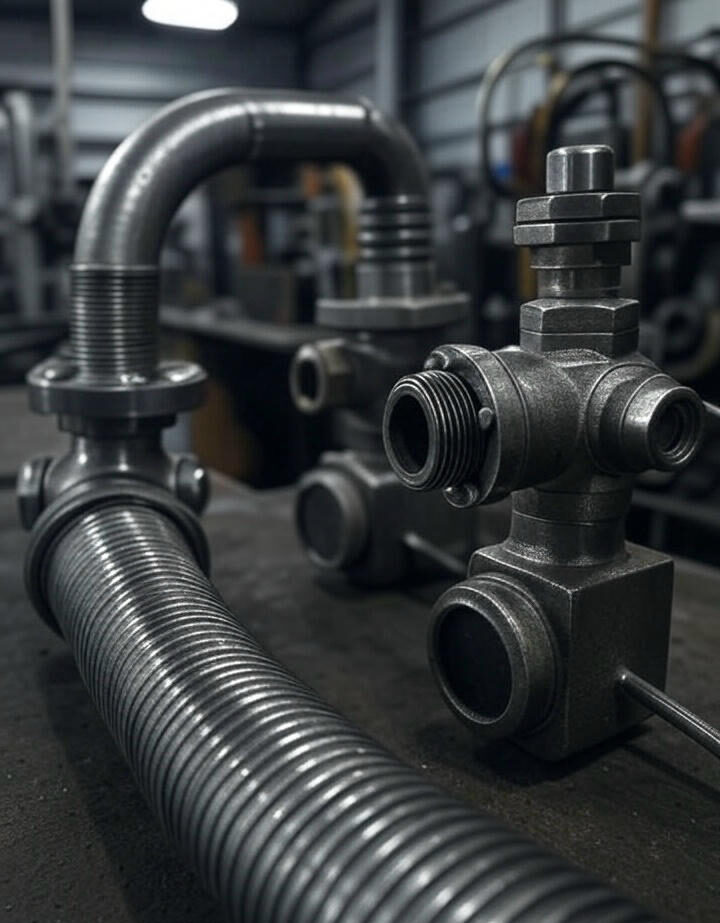
TANKS
- Types: Raw Water Tanks, Treated Water Tanks, Fuel Storage, Chemical Dosing Tanks
- Capacities: From 1 KL to 100 KL (customized)
- Material: MS, SS 304/316, FRP-lined MS
- Orientation: Horizontal or vertical, with or without stand/skid
- Complete with manholes, level gauges, vent nozzles, drain valves
- Sandblasted and painted or epoxy-coated internally
- Available with insulation and cladding on request
- Skid-mounted versions available for modular plants
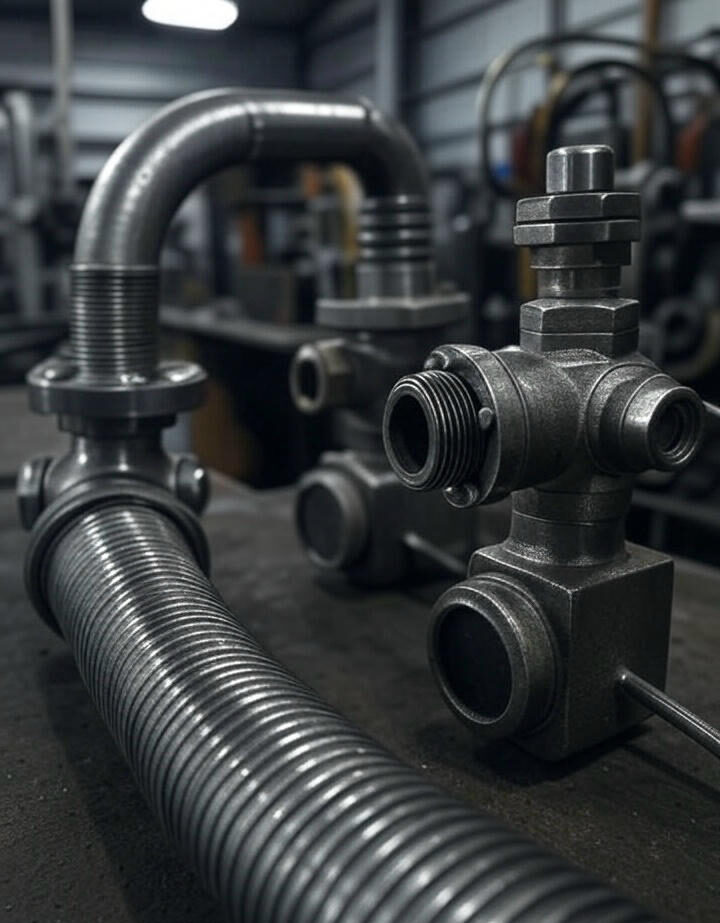
STRUCTURE
- Scope: Boiler supporting structures, platforms, walkways, staircases, ducts & hopper supports
- Material Grades: IS 2062 Gr. A/B/C, Galvanized Steel (where required)
- Finish: Painted with red oxide primer, PU/Epoxy topcoat, or hot-dip galvanized
- Fabrication: CNC profile cutting, MIG/SMAW welding, shot-blasting
- Designed as per IS 800 / IS 875 / MBMA / Eurocode
- Modular and bolt-assembled design for ease of erection
- Integrated cable trays, pipe racks, and access ladders
- Structural stability for high-wind, high-load industrial environments
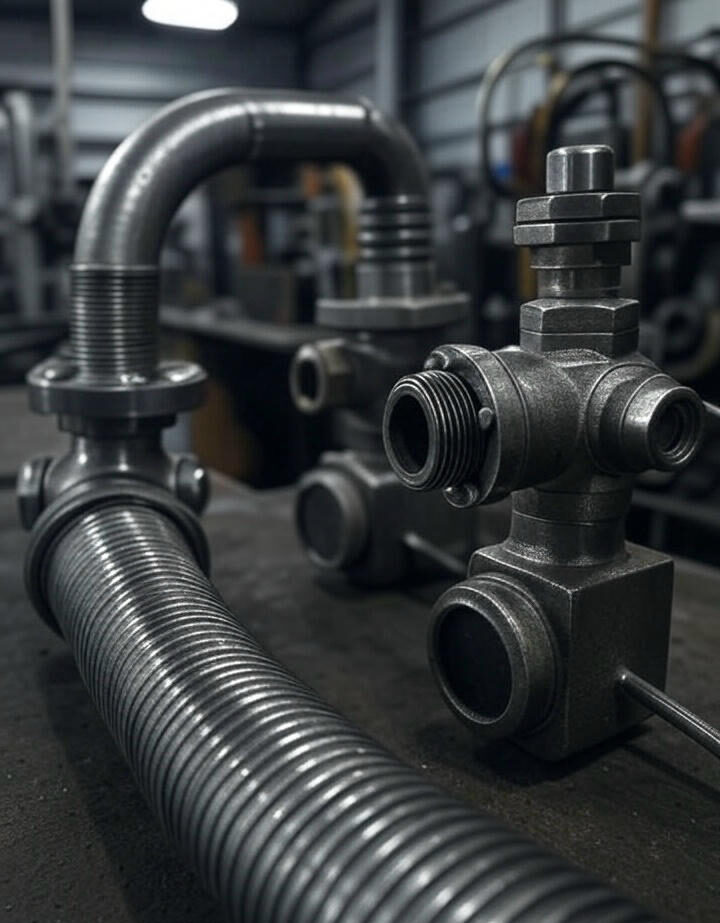
OTHER
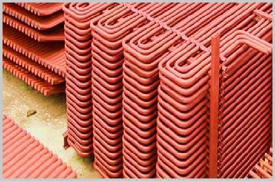
SPARES
TUBE/PIPE
VALVES
COILS
Studded In-Bed Coils
Economizer Coils
Super-Heater Coils
VESSEL
NON-PRESSURE PARTS
TUBE/PIPE
SILENCER
TANK
STRUCTURE
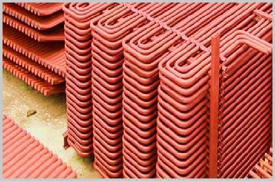
SPARES
-
PRESSURE PARTS
- NON-PRESSURE PARTS
- TUBE/PIPE
- VALVES
- COILS
- VESSEL
TUBE/PIPE
– Water walls / Furnace Tubes: SA 210 Gr A1/Gr C, SA 192, SA 106 Gr B, SA 213 T11/T22, SS 304/316
– Superheater / Reheater: SA 213 T11/T22/T91, SS 304H, SS 321, SS 347H
– Economizers: SA 210 Gr A1/Gr C, SA 106 Gr B, ASTM A179, ASTM ERW A53 Gr B, SA 213 T11/T22, SS 304/316/321
– Steam Headers: SA 106 Gr B/Gr C, SA 335 P11/P22/P91, SS 304H, SS 321, SS 347H
– Feedwater Piping: SS 304 / 316, A106/SA106 Gr B/C, SA 210 Gr C, ASTM A53 Gr B ERW, SA 335 P11/P22/P91, SS 304/316/321, SS 347H
– Steamline: SA 106 Gr B/Gr C, SA 335 P11/P22/P91, SS 304H/321/347H
All boiler tubes and pipes supplied by PP Boilers conform to stringent international and national codes, including:
ASME Section I & VIII
ASTM A213, A335, A106
DIN EN10216/10217
IBR (Indian Boiler Regulations) – with third-party inspection and stamping where applicable
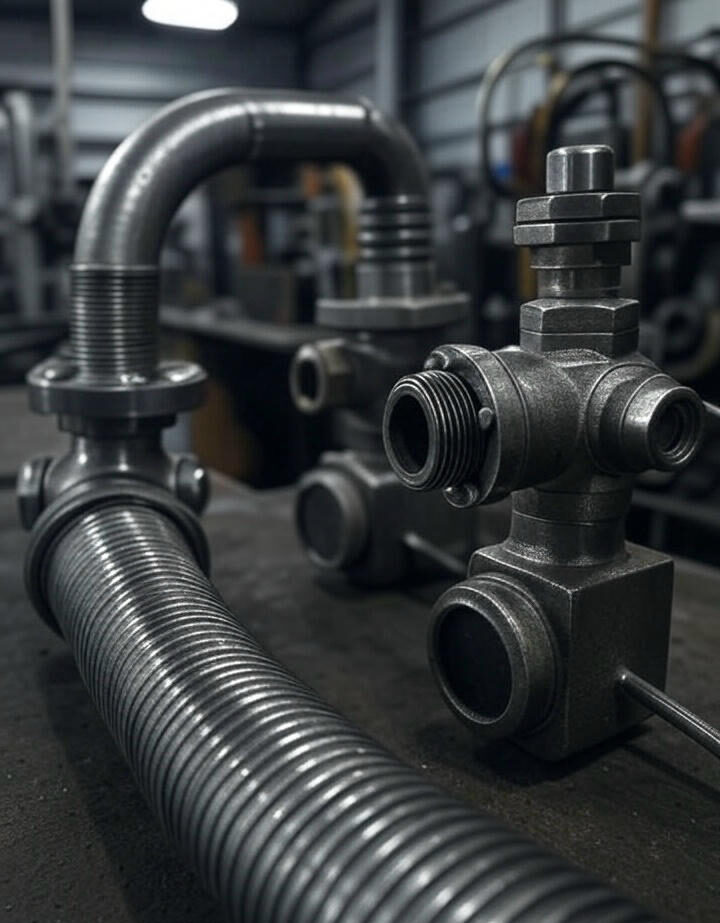
TUBE/PIPE
– Water walls / Furnace Tubes: SA 210 Gr A1/Gr C, SA 192, SA 106 Gr B, SA 213 T11/T22, SS 304/316
– Superheater / Reheater: SA 213 T11/T22/T91, SS 304H, SS 321, SS 347H
– Economizers: SA 210 Gr A1/Gr C, SA 106 Gr B, ASTM A179, ASTM ERW A53 Gr B, SA 213 T11/T22, SS 304/316/321
– Steam Headers: SA 106 Gr B/Gr C, SA 335 P11/P22/P91, SS 304H, SS 321, SS 347H
– Feedwater Piping: SS 304 / 316, A106/SA106 Gr B/C, SA 210 Gr C, ASTM A53 Gr B ERW, SA 335 P11/P22/P91, SS 304/316/321, SS 347H
– Steamline: SA 106 Gr B/Gr C, SA 335 P11/P22/P91, SS 304H/321/347H
All boiler tubes and pipes supplied by PP Boilers conform to stringent international and national codes, including:
ASME Section I & VIII
ASTM A213, A335, A106
DIN EN10216/10217
IBR (Indian Boiler Regulations) – with third-party inspection and stamping where applicable
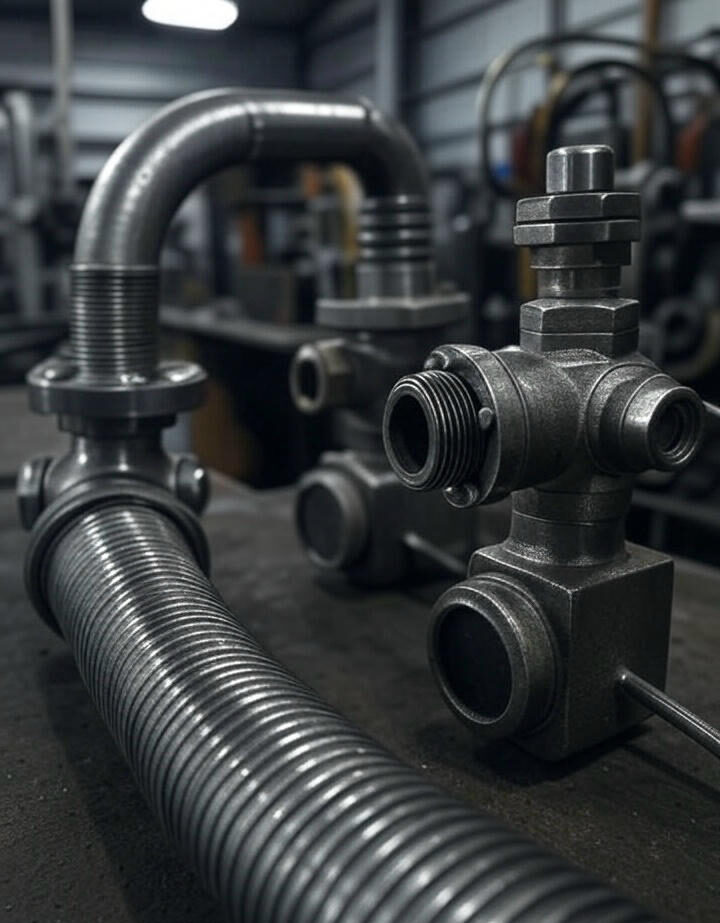
VALVES
Categories & Specifications:
- Gate Valve
- Globe Valve
- Ball Valve
- Butterfly Valve
- Plug Valve
- Pneumatic Globe Control Valve
- Pneumatic Ball Valve
- Pneumatic Butterfly Valve
- Motorized Gate and Globe Valve
- Motorized Ball Valve
3. Motorized (Electric) Valves:
- Motorized Gate and Globe Valves
- Motorized Ball Valves
4. Safety & Relief Valves:
- Spring-Loaded Safety Valves
- Pilot-Operated Valves
- Thermal Relief Valves
- Spring-Loaded Safety Valve
- Pilot-Operated Valve
- Thermal Relief Valve
- Lift Check & Swing Check Valve
- Non-Return Valve
6. Blowdown Valves:
- Quick-Opening Blowdown Valve
- Continuous Blowdown Control Valve
- Pressure Classes: ANSI 125#, 150#, 300#, 600#, 900#, 1500#, 2500# (selection based on operating conditions).
- End Connections: Flanged (RF, RTJ), Butt Weld, Socket Weld.
- Design Standards: ASME B16.34, API 600, API 602, API 603, BS 1873, IBR compliance.
- Materials: WCB, WC6, WC9, C5, C12A, SS 304/316/321/347, P11, P22, high-temp alloys.
- Trim & Seat Materials: Stainless steel, Stellite-faced, and PTFE options for erosion and temperature resistance.
- Leakage Classes: API Class IV, V, VI, with control valves rated as Class V+ for precise flow control.
- Actuations: Manual, pneumatic, electric motorized, optional hydraulic.
- Fire Safe Design: Conforms with API 607 for fuel/gas services.
All valves are rigorously tested per API 598 standards, ensuring performance, safety, and long service life across diverse boiler applications. Customization in sizes, end connections, and actuation options is available to meet specific project requirements.
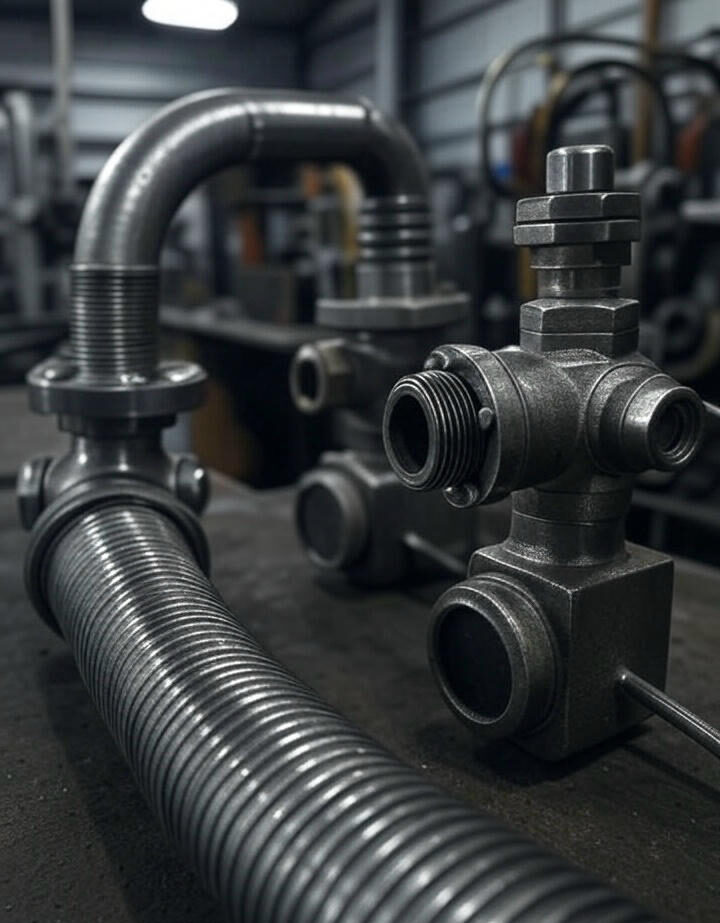
COILS
PP Boilers specializes in the design, fabrication, and supply of high-performance boiler coils engineered to meet the demanding thermal and mechanical requirements of modern industrial boilers. Our range includes Studded In-Bed Coils, Economizer Coils, and Superheater Coils, each tailored for specific zones within the boiler system to maximize heat transfer, reliability, and efficiency.
Boiler Bed Coils (Fluidized Bed Coils / Bed Evaporators)
Studded In-Bed Coils are critical heat transfer elements embedded within the fluidized bed of AFBC boilers. Designed to operate under high-temperature, high-erosion environments, these coils efficiently extract heat from combusting bed material and transfer it to the working fluid (water/steam). Their studded surface significantly increases the effective heat transfer area and sustains fluidization within the bed.
Design & Construction:
- Constructed from high-grade materials including ASTM A106 Gr. B, A192, SA 210 Gr. C, and stainless steels like SS 304/316
- Tube OD: 25 to 63.5 mm, with wall thicknesses optimized for high-pressure service
- Studs/Fins: Welded MS or SS304 studs to improve heat transfer and protect against erosion
- Surface-treated for resistance to corrosion, erosion, and scaling
- Absorbs direct heat from hot bed material to produce saturated steam
- Promotes stable fluidization essential for efficient combustion
- Helps maintain uniform bed temperature, improving thermal efficiency and combustion control
- Enhances boiler responsiveness during fluctuating load conditions
Performance & Advantages:
- Engineered for long service life under abrasive and cyclic thermal loads
- High thermal conductivity and mechanical strength ensure reliable operation
- Custom-designed for specific boiler capacities and fuel types
- Supports rapid steam generation and efficient load response
- Compliant with ASME Section I, IBR, and client-specific requirements
Economizer coils are integral heat recovery components located in the flue gas path of a boiler. Their primary function is to preheat feedwater before it enters the boiler drum, utilizing residual heat from exhaust gases. This process significantly improves boiler thermal efficiency, reduces fuel consumption, and lowers operational costs. PP Boilers offers custom-engineered economizer coils designed for long-term performance in high-temperature, corrosive environments.
Design & Construction:
- Manufactured using carbon steels like ASTM A106 Gr. B, A179, or A210, and available in low-alloy grades for higher temperature applications
- Tubes configured in bare or finned arrangements to maximize surface area and heat exchange efficiency
- Available in horizontal or vertical coil banks based on space and gas flow direction
- Coil sizes and arrangements are optimized for flue gas temperature, feedwater flow, and pressure drop limitations
- Fabricated as seamless or welded tube assemblies in compliance with ASME and IBR standards
Functions:
- Recovers waste heat from flue gases to raise feedwater temperature
- Reduces the energy required for steam generation by decreasing the enthalpy gap
- Lowers exit flue gas temperature, reducing heat loss through the stack
- Contributes to lower fuel usage and enhanced boiler efficiency (typically by 3–7%)
- Designed for corrosive and high-temperature flue gas environments
- Enhances thermal efficiency and reduces fuel costs
- Prolongs boiler life by minimizing thermal shock and condensation in the economizer zone
- Available with soot blowers or access ports for ease of cleaning and maintenance
- Fully compliant with IBR, ASME Section I, and customer-specific engineering standards
Superheater Coils are critical heat transfer components installed in the convective or radiant zones of a boiler to convert saturated steam into superheated steam. This process increases the thermal energy of the steam, enhancing overall plant efficiency, especially in power generation and high-temperature process applications. PP Boilers manufactures robust, high-performance superheater coils tailored to withstand extreme temperatures, high pressures, and cyclic thermal loads.
- Fabricated from high-temperature alloy steels such as SA213 T11, T22, T91, TP304, TP347H, or stainless steels like SS 304/316, based on operating pressure and temperature
- Available in U-bend, serpentine, and pendant-type coil configurations to suit radiant or convective placement
- Designed for steam temperatures up to 540°C or higher, with pressure ratings exceeding 100 kg/cm²
- Seamless or welded tube construction per ASME Section I, IBR, and customer-specific design codes
- Provision for expansion loops and flexible coil supports to absorb thermal expansion
- Increases the temperature of saturated steam without increasing pressure
- Supplies superheated steam to turbines or process units for improved energy efficiency
- Prevents steam condensation during transport and expansion in turbines
- Enhances heat recovery and thermal performance in power boilers and industrial steam systems
- High thermal conductivity and corrosion resistance for extended operating life
- Optimized coil geometry for uniform heat absorption and reduced metal temperature stresses
- Compatible with fluidized bed, travelling grate, and oil/gas-fired boilers
- Integrated with temperature control systems for precise outlet steam temperature
- Offered with soot blower provisions to maintain clean heat transfer surfaces
- Compliant with ASME, IBR, and ISO standards, ensuring safety and reliability
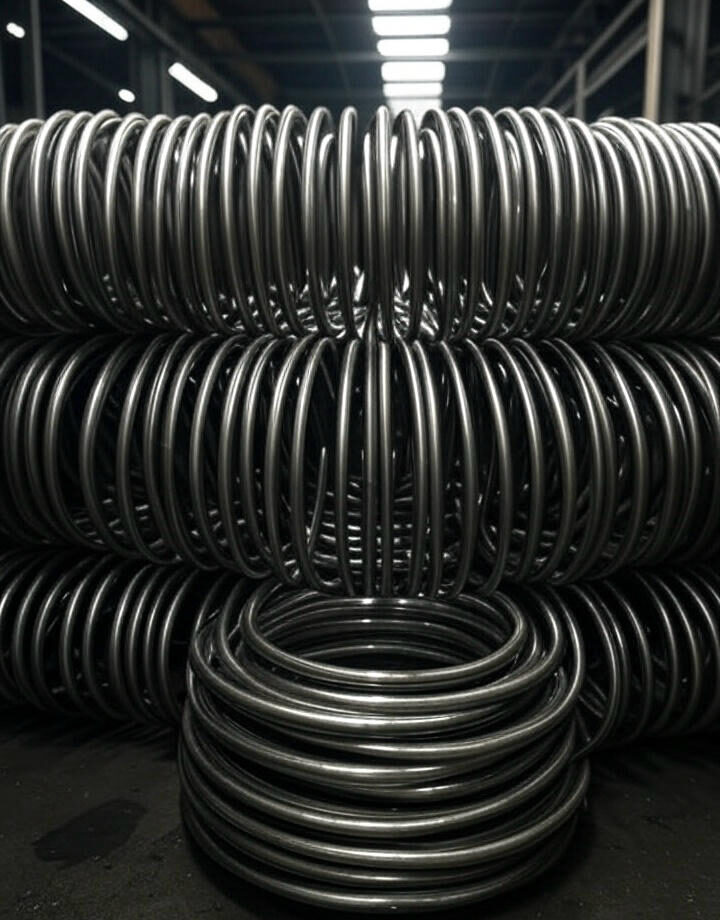
VESSEL
PP Boilers designs and fabricates a complete range of custom-engineered pressure vessels for high-pressure and high-temperature boiler applications. Built to comply with global codes and optimized for reliability and safety, our pressure vessels are integral to the performance of AFBC, CFBC, WHRB and other high-capacity and process boilers.
We offer fully fabricated and IBR-stamped pressure vessels for:
Steam Drum:
Mud Drum:
- Positioned at the bottom to collect sludge and heavy impuritie
- MOC: SA 516 Gr.70, IS 2002, SA 105 flange
- Serve as steam and water manifolds for coil circuits
- MOC: SA 106 Gr. B/C, SA 335 P11/P22/P91, SS 304H/321/347H
- Used to remove dissolved gases from feedwater
- Spray & tray-type available
- MOC: SA 516 Gr.70, SS 304/316 for wetted parts
- Designed to safely discharge boiler blowdown under pressure
- MOC: SA 516 Gr.60/70, with optional refractory lining
- For storing and releasing saturated steam during fluctuating loads
- MOC: SA 516 Gr.70, with suitable insulation and accessories
Design & Code Compliance:
All pressure vessels by PP Boilers are designed as per:
- ASME Section I / Section VIII Div.1
- IBR – Indian Boiler Regulations
- ISO 9001:2015 Quality System
Vessels are supplied with:
- Full NDT testing: Radiography, Hydrotest, UT, MPT
- IBR certification with stamping and form I
- TPI approval from Lloyd’s, TUV, SGS, or as per client requirement
- Diameter Range: 300 mm to 3500 mm
- Design Pressure: Up to 100 kg/cm²
- Design Temperature: Up to 550°C
- Shell Thickness: 10 mm to 80 mm
- Material Options: Carbon Steel, Alloy Steel, Stainless Steel (304, 316, 321, 347H), P11, P22, P91 etc.
Salient Features of Our Pressure Vessels:
- Heavy-duty construction for long life under cyclic and steady-state loads
- High-precision machining of nozzle connections and welding bevels
- Corrosion-resistant internal finishes or claddings available on request
- Fully customizable for layout, nozzle orientation, saddle/base support
- Pre-insulated and cladded supply available for field-ready installation
- Sourced only from Boiler Quality Plates (BQP) with test certificates
- Designed for low maintenance, maximum safety, and thermal efficiency
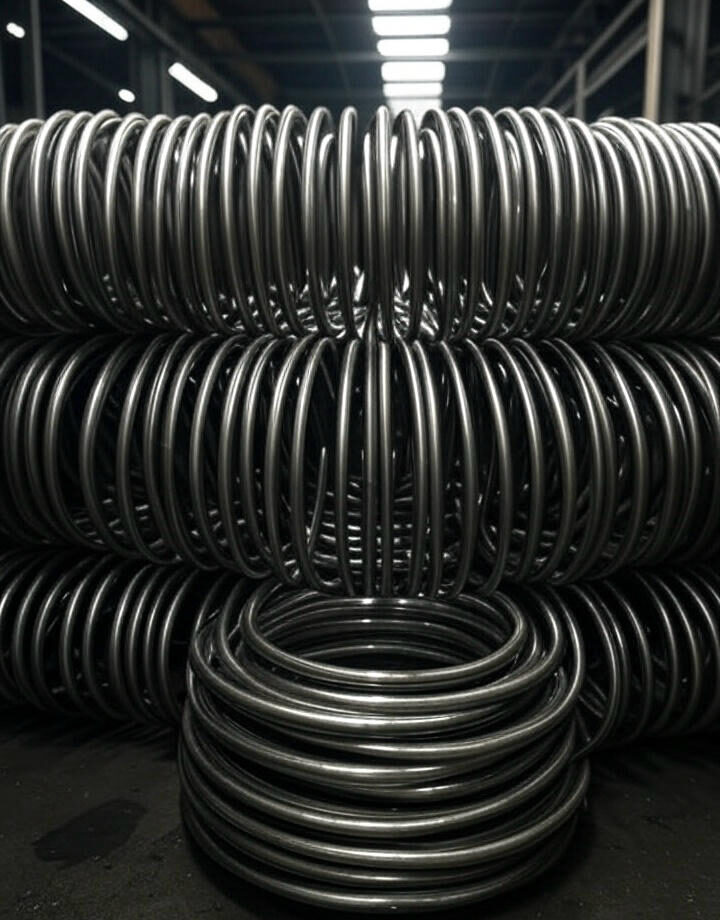
- TUBE / PIPE (Non-IBR)
- SILENCER
- TANKS
- STRUCTURE
TUBE/PIPE (Non-IBR)
We supply high-quality tubes and pipes for non-pressure applications such as ducting, sootblower lances, drain piping, insulation support, and non-process utilities.
- Material Grades: MS, IS 1239, ASTM A106, ERW IS 3589, SS 304/316
- Sizes: ½” to 20″ NB; schedule 10 to 80
- Types: Seamless, ERW, galvanized, or pickled
- Applications: Non-IBR piping, ductwork, expansion loops, instrumentation air lines
Key Features:
- Accurate tolerances and smooth internal finish
- Available with plain, threaded, flanged, or beveled ends
- Surface coating options: painted, epoxy, or zinc
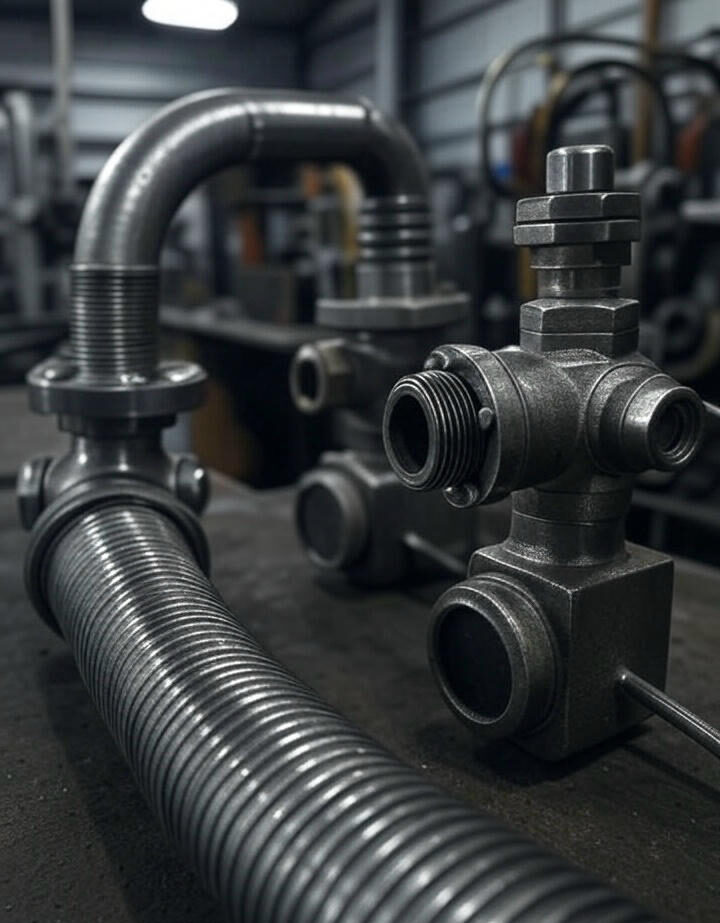
SILENCER
- Types: Vent Silencer, Blow-off Silencer, Safety Valve Silencer
- Material: Carbon steel or stainless steel (internals), MS outer casing
- Design Pressure: Atmospheric to 150 kg/cm²
- Noise Reduction: Up to 40–50 dB(A) depending on application
Key Features:
- Multi-stage acoustic diffusers with absorbent lining
- Designed for zero backpressure and high-velocity exhaust
- Flanged or welded end connections
- Supplied with lifting lugs, weather hoods, and drain traps
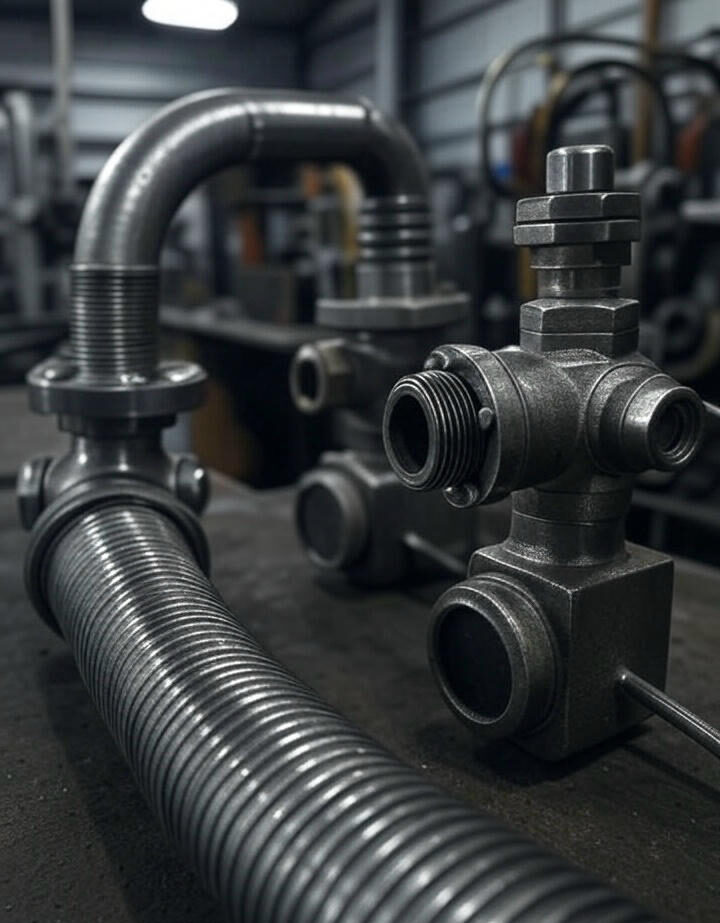
TANKS
- Types: Raw Water Tanks, Treated Water Tanks, Fuel Storage, Chemical Dosing Tanks
- Capacities: From 1 KL to 100 KL (customized)
- Material: MS, SS 304/316, FRP-lined MS
- Orientation: Horizontal or vertical, with or without stand/skid
- Complete with manholes, level gauges, vent nozzles, drain valves
- Sandblasted and painted or epoxy-coated internally
- Available with insulation and cladding on request
- Skid-mounted versions available for modular plants
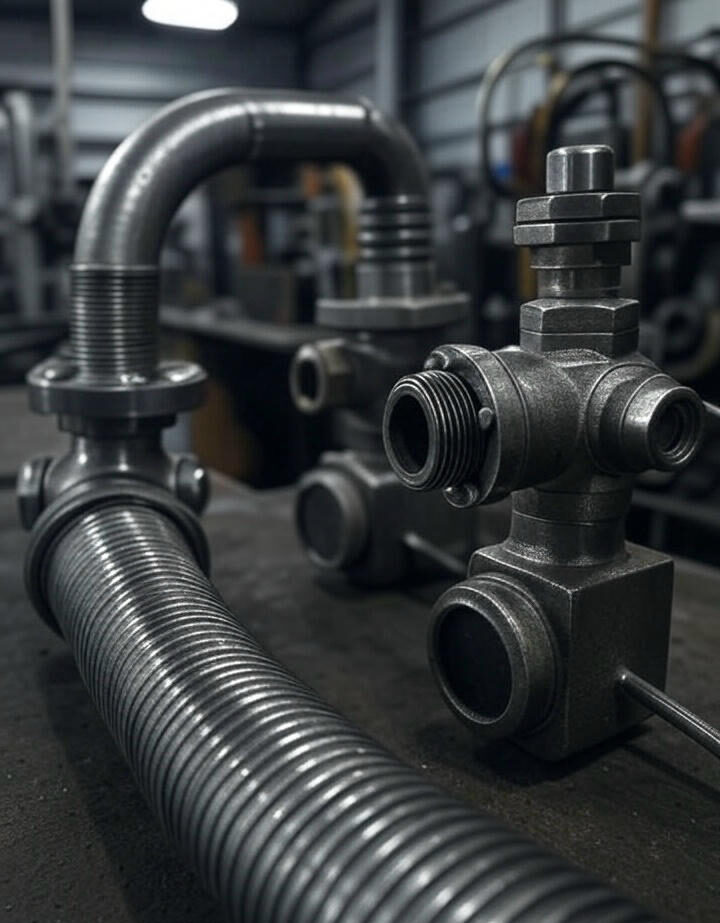
STRUCTURE
- Scope: Boiler supporting structures, platforms, walkways, staircases, ducts & hopper supports
- Material Grades: IS 2062 Gr. A/B/C, Galvanized Steel (where required)
- Finish: Painted with red oxide primer, PU/Epoxy topcoat, or hot-dip galvanized
- Fabrication: CNC profile cutting, MIG/SMAW welding, shot-blasting
- Designed as per IS 800 / IS 875 / MBMA / Eurocode
- Modular and bolt-assembled design for ease of erection
- Integrated cable trays, pipe racks, and access ladders
- Structural stability for high-wind, high-load industrial environments
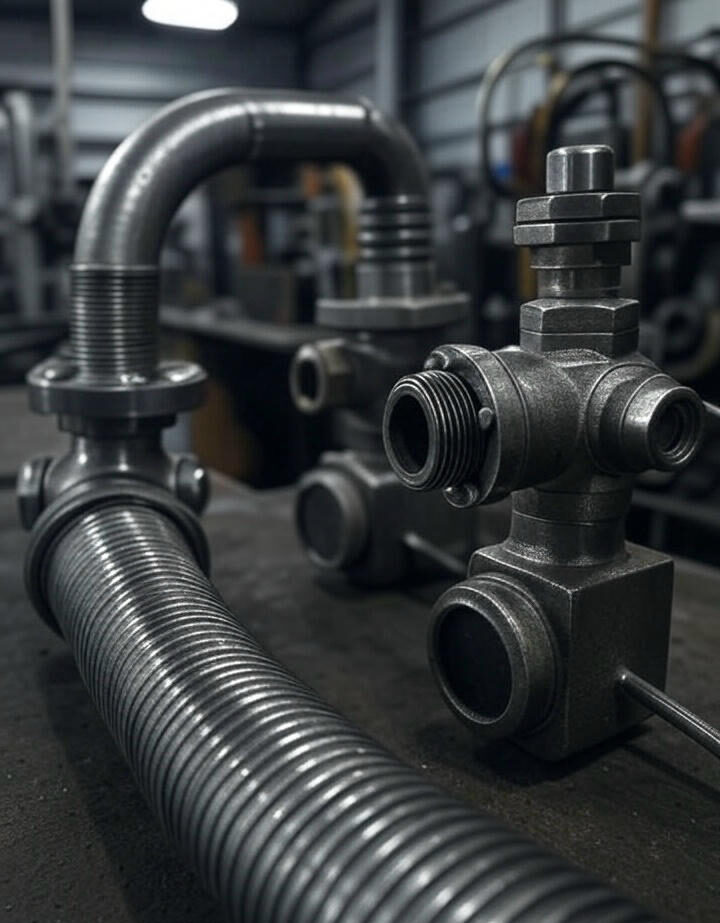